Technology
The Value of Cobots in the Manufacturing Process
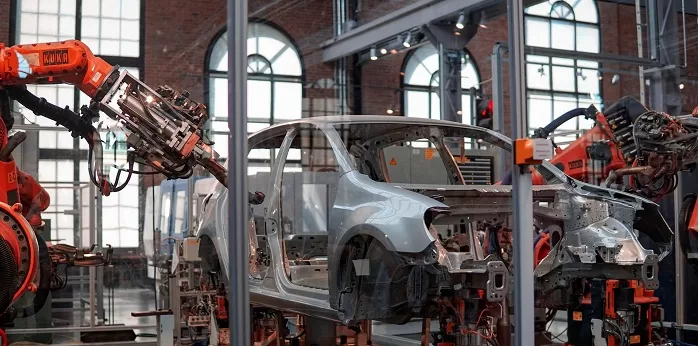
A close relative to the robotic arm, the collaborative robot has been a stand-out performer in the quest to improve human-machine interactions. Unlike mass production robots, this mechanical arm has revolutionized industrial production without replacing human labor. Since its launch in 2004, the cobot has improved manufacturing processes and made it possible for humans and machines to work together.
What You Need to Know
Cobots are motor-driven robot arms designed to do redundant tasks faster and with better precision. They contain several safety features that make them ideal for low-level projects. These mechanical arms integrate seamlessly into factory operations and improve output. A collaborative robot is a futuristic technology that shows digital automation at the peak of its powers.
The concept of machine learning is a critical development in collaborative robot technology. Manufacturers are now focusing their efforts on designing mechanical arms that are fully automated. The improvement in AI and automation technology has improved rapidly and given these robots the ability to perform intricate tasks. Collaborative robots are no longer limited to low-level tasks. Modern varieties perform complex jobs such as orthopedic and open heart surgery. This process is possible because robots work faster and are more precise.
The evolution of collaborative robots has made this technology a leader in industrial manufacturing. Factories now have a better output, and they are able to maintain product quality. Factories have not achieved full automation yet. The current state of this technology shows that it improves production efficiency by almost 80%.
Cobots: Top Industrial Applications
The robotics industry has grown tremendously in the past two decades. Many of these mechanical arms worked primarily for pick-and-place functions. As new systems emerge, the need for diversification has led to more intricate and better functioning collaborative robots. Modern varieties have several applications. Manufacturers can use these robots for simple packaging jobs and complex assembling tasks. Some of the notable functions include.
Palletizing
This process is similar to packaging and preparing products for shipping. Power limiting and other safety protocols have made cobots capable of handling fragile equipment without damaging any components. Palletizing involves moving, packaging, and labeling products for shipping. This task is risky for humans, especially if it involves heavy lifting or fragile goods. Cobots can be programmed to handle hazardous materials and make them ready for delivery.
Collaborative robots work faster and more efficiently. Tasks that are difficult for humans to perform are delegated to these mechanical arms. Note that this equipment works in relatively tight spaces. This means that small and medium enterprises get the benefit of industrial automation. This practice takes the cost-intensive element off the table as an advantage. Modern cobots are compact and have a high payload. They can lift heavy objects around factories with limited floor space.
Another perk is that cobots work together with humans. They have several sensors that help them maintain optimal safety in the workplace. It is impossible for an employee to collide with a robot because they automatically switch off when someone is in close proximity.
Machine Tending
This futuristic technology has eliminated the limitations of traditional robots. The tasks involved go beyond the confines of simple material handling. A cobot can identify and replace faulty machine parts. The machine learning involved in this process enables them to monitor equipment functioning and point out problems in the production chain. They use Artificial Intelligence to initiate and stop factory functions. Scheduling and task simplification capabilities make these mechanical arms critical to factory floor functionality.
The use of computer numerical control is also a feature worth mentioning. CNC controls the movement of factory machinery. It is a system that can accomplish several tasks simultaneously. A collaborative robot controls factory tools and prompts the necessary action. This process uses pre-programmed digital automation to make the production floor more efficient.
Assembly and Welding
Cobots have evolved from garden variety pick and place functions to tasks that require precision. Welding and assembly lines are the latest jobs, especially for tasks that need accuracy. Robots are accurate to within a percentage point. This property makes them ideal for intricate welding and assembly tasks. The fundamental aim of any manufacturer is consistency in product quality. You must produce each component with the exact cuts and dimensions. The precision of cobots reduces material waste and maintains manufacturing efficiency.
While skilled welders and assemblers are at the top of the food chain for various tasks, cobots work faster. Currently, these robots perform low-volume projects. As manufacturers create better technology, it is only a matter of time before robots begin operating in mass-producing factories.
Quality Inspection
Cobots do more than relieve humans from exhausting and dangerous tasks. The programming involved functions to ensure everything is operating at optimal capacity. Cobots create an efficient network of operations. According to the Comprehensive Logistics Unit, collaborative robots can perform machine inspection and other quality assurance functions. They can also detect defects in your products and help rectify the manufacturing process.
Collaborative robots have inspection software that evaluates the production process and streamlines automation. The aim of this technology is to improve industrial strength and establish uniformity. Using hand tools like tape measures causes inconsistency in many products. Before the products make it to the market, the function of these robots is to identify discrepancies and correct them. They also improve the manufacturing process by reducing the time needed to complete production.
A collaborative robot is a critical part of the production process. It ensures all your products are the same and the quality is maintained. Even with experienced personnel, the chances of mistakes are a genuine concern. Robots reduce this risk and improve production by 79%.
Bottom Line
Cobots have several benefits. They do not require a large workspace. They are safe and specifically designed to work with humans. The technology used is dependable, and the results are tangible. They have many intelligent features that make them ideal for any industrial function. Manufacturers are encouraged to consider collaborative robots as a valuable inclusion to compete at the top level. It is a system that guarantees a return on investment.