Auto
Electrifying Luxury: Production Launch of The New BMW 7 Series in Dingolfing
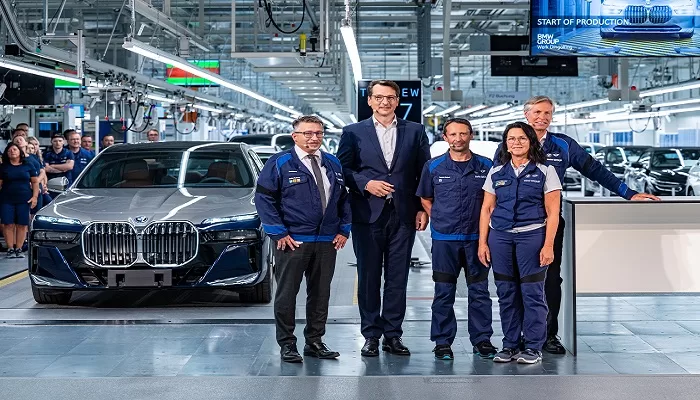
The first series-produced vehicles of the new BMW 7 Series have rolled off the production lines of BMW Group Plant Dingolfing. In fact, it was a double debut, with the new top-of-the-range BMW manufactured not only with highly efficient combustion engines but also as the fully electric BMW i7. Milan Nedeljković, BMW AG Board Member for Production: “Our new BMW 7 Series is the first luxury sedan in the world to offer customers a choice between three types of drive. Whether fully electric, combustion-powered or, soon, plug-in hybrid, we have the flexible production structures and outstanding integration skills we need to manufacture such a diverse range of drives efficiently.”
Over €300 million invested in Dingolfing vehicle plant
The BMW Group invested over €300 million to ready the Dingolfing vehicle plant for production of the new BMW 7 Series. As it strives consistently to implement the BMW vision of production of the future, its largest European plant is increasingly being transformed into a BMW iFACTORY practising the ‘Lean. Green. Digital.’ approach. For the first time, the BMW Group is piloting automated manoeuvres within the production environment by just-made BMW 7 Series vehicles – and optimising assembly and outbound logistics processes as a result.
BMW i7: The latest milestone on the road to e-mobility in the luxury segment
With production under way, once sales organisations have been provided with the show and demonstration vehicles they need, the new BMW 7 Series will be available to customers worldwide in the autumn of this year. The BMW i7, especially, marks the next step in the BMW Group’s electromobility campaign for the luxury segment, which Dingolfing has come to symbolise. Board Member Milan Nedeljković: “Exactly a year ago, we were here to celebrate the start of production of our BMW iX. the BMW i7 is the latest milestone on our journey. Next year will see the launch of the fully electric variant of the BMW 5 Series as we step up the pace of electromobility and electrify our core model series.” By the end of 2022, one in four BMWs leaving Dingolfing is already expected to incorporate an electric drive, rising to approx. 50 percent of the plant’s total output by the middle of this decade, according to current plans.
100 percent exchange flexibility between different types of drive
The new BMW 7 Series is assembled on the same line as the BMW 5 Series, 8 Series and the fully electric BMW iX. “We are 100 percent flexible and able to switch between drive variants for the BMW 7 Series,” explained Christoph Schröder, Plant Director. “This means we can manufacture completely in line with demand for the various drives and use our plant capacity as fully as possible.”
BMW 7 Series benefits from product and process modules of the BMW iX
The new BMW 7 Series builds on various technology modules of the BMW iX – not just for individual features like the onboard network architecture, user interface and driver assistance systems but also in terms of production and validation processes in assembly, for which the BMW iX was the trailblazer. Examples include the redesigned aggregate fitting station, sling loop assembly, test rigs for driver assistance systems and the new finish process, which is now even more efficient throughout, from first ignition to the vehicle dispatch area. The BMW iX is currently one of Dingolfing’s most successful vehicles.
Re-using systems, plus the special two-tone paint process
Converted during production shutdowns, the bodyshop was able to integrate the new BMW 7 Series into the structures previously used to manufacture the model’s predecessor. By adapting and re-using systems in this way, the BMW Group has saved hundreds of millions of euros and a wealth of resources. The floor assemblies of the new BMW 7 Series have distinct geometries and vary in part, depending on the type of drive, yet they can all be manufactured completely flexibly in any combination on one and the same main production line. In addition, automation – in door fitting, for instance – and a reduction in material combinations and the bonding processes required have made processes more efficient. In the paintshop, a special process has been established for the exclusive two-tone paintwork of the new BMW 7 Series, melding techniques from series production with the manual painting skills of the Dingolfing specialists.
Inhouse production of e-drive components
The e-drive components of the BMW i7 – specifically the high-voltage battery and highly integrated electric drive – are also made in Dingolfing. Like those of the BMW iX, BMW i4 and BMW iX3, they are manufactured nearby, in the BMW Group Competence Centre for e-Drive Production.
Recently the Competence Centre launched two new production lines, enabling the facility to produce sufficient e-drives for more than 500,000 electric cars a year. The workforce has also increased, from approx. 600 in early 2020 to over 2,300 today.
“The transformation to a BMW iFACTORY is well under way”
“With their breakthrough technologies, vehicles like the BMW 7 Series are catalysts for change – including in our plants,” emphasised Milan Nedeljković, pointing out that they involve innovations not only in the product but also in production. “Dingolfing’s transformation into a BMW iFACTORY is well under way,” added Christoph Schröder. “We have hundreds of employees working to make our plant more efficient, flexible and sustainable, with effective innovations and digitalisation solutions as the key drivers of progress.”
The Lean. Green. Digital. approach of the BMW iFACTORY is already a reality in the production halls of Plant Dingolfing.
Lean. Flexibility and the widespread rollout of smart logistics solutions
The aspect of Lean is being realised at Plant Dingolfing to a large degree by the flexible layout of production structures. “Our structures give us the exchange flexibility we need to switch between different models and drive types, the volume flexibility to react quickly to radically fluctuating demand, and the order flexibility to accommodate the last-minute changes customers can request up to just a few days before their car is produced. Here in Dingolfing, flexibility is simply a part of our DNA,” said Christoph Schröder.
Another example of how digitalisation supports the efficiency goals of Plant Dingolfing is the comprehensive rollout of smart logistics solutions. Dingolfing is the company pioneer in this regard, operating not only automated forklifts but also autonomous tug trains, automated outdoor logistics solutions and smart transport robots (STRs) that carry parts to the line-side. Made by the BMW Group subsidiary Idealworks, STRs are expected to more than double in number to over 200 by the end of 2022 as series production of the BMW 7 Series ramps up. “Thanks to flexible, automated solutions like this, we have become extremely efficient at managing the complexity and myriad part numbers we work with here at the plant,” said Schröder.
Green. Investing in sustainable production
The Green aspect of the BMW iFACTORY and sustainable production in Plant Dingolfing is realised by a range of measures. These include sourcing 100 percent green energy, re-using several hundred existing production robots in the bodyshop, and reducing the consumption of resources in the paintshop. Here, investments of over €50 million are currently being made in new cathodic dip lines and a dry separation system, which will save significant amounts of water and energy. In addition, the waste heat from the drying furnaces will no longer be used purely as process heat but also to generate electricity.
Other facets of sustainable production include energy-efficient systems, packaging planning, traffic logistics, recycling and water management. On-site transportation, for example, is carried out by electric truck. Also, Dingolfing currently has a recycling quota of more than 90 percent and an even higher re-use quota of more than 99 percent. In 2021, this sent total residual waste tumbling to just 580 grams per car produced. And when it comes to water, Dingolfing currently covers 40 percent of its needs by drawing on its own source, thereby helping to preserve the region’s drinking water supplies as well.
Digital. Automated quality control by cameras with AI
Intelligent digital solutions are used in all areas of production at BMW Group Plant Dingolfing, but especially in vehicle assembly – be it for virtual training, smart scanners, automated AI-based quality control or automated driving by freshly manufactured vehicles.
When it comes to AI, the BMW Group has proven its pioneering credentials with its AIQX (Artificial Intelligence Quality Next) project, which uses sensors and AI to automate quality processes. Smart camera systems and sensors embedded in the production lines record data for backend evaluation in real-time using algorithms and AI. Feedback is then sent directly to employees on the line, via their smart devices. AIQX can be used to determine variants, verify completeness and detect any anomalies that may have occurred during fitting. It is currently operating in 40 applications in production of the new BMW 7 Series.
The launch of the latest vehicle has also boosted the number of use cases of IPS-i. This digitalisation project uses an IT platform to converge data from a wide range of location systems and generate a digital twin in real-time of the assembly hall. From the use of smart scanners and screwdrivers to RFID-based verification of the allocation of parts to vehicles, the IPS-i platform provides the basis for locating and interconnecting every item – every vehicle, component and tool – involved in the production process. With the new BMW 7 Series, RFID-based component tracing alone has been extended to 45 different part families.
BMW 7 Series pilots automated driving within plant
Production of the new 7 Series also uses a digital innovation with major potential for assembly and outbound logistics in BMW Group plants and distribution centres: automated driving in-plant (‘automatisiertes Fahren im Werk’, AFW). As part of the digitalisation strategy, the AFW project will be piloted in Dingolfing from July and sees newly produced BMW 7 Series drive automatically along a 170-metre route from the first ignition and initial testing area in assembly to the finish area in the plant. The same method will be used to get vehicles from the end of the finish line to the dispatch area.
The AFW project was developed by the BMW Group and the two startups Seoul Robotics and Embotech, who provide the software and technology. Project manager Sascha Andree explained: “Automated driving within the plant is fundamentally different from autonomous driving for customers. It uses a completely different system. So instead of relying on the vehicle’s sensors, it uses an infrastructure outside the car to enable environment recognition and plan the vehicle’s movements.” The route through the logistics areas of the plant is fitted with sensors that use Seoul Robotics software to generate data for vehicle localisation and environment recognition. Further externally based drive-planning software, by Embotech, then steers, brakes, accelerates and parks the driverless vehicles by sending them the relevant commands.
AFW is expected to be piloted until 2023 and will initially be rolled out on other models at Plant Dingolfing as well.
Dingolfing – Home of the BMW 7 Series since 1977
Plant Dingolfing, in Lower Bavaria, has been the home of the flagship BMW 7 Series since 1977 and is now manufacturing the seventh generation. It is the BMW Group’s lead plant for large BMWs and has extensive expertise in production launches as well as decades of experience in the manufacture of premium vehicles for the luxury class. To date, Plant Dingolfing has manufactured a grand total of more than 11 million BMW cars, and a further production milestone is on the schedule this year: the two millionth BMW 7 Series.
BMW Group Plant Dingolfing – Key facts.
Plant Dingolfing is one of the BMW Group’s more than 30 production sites around the world and its largest in Europe. Every day around 1,600 BMW 4 Series, 5 Series, 6 Series, 7 Series, 8 Series and all-new, fully electric BMW iX vehicles roll off the production lines in car plant 02.40. In 2021, annual output totalled some 245,000 units.
The site currently employs approx. 17,000 people. It is also training about 850 apprentices for 15 professions, making it the largest training organisation in the BMW Group.
Dingolfing manufactures not only cars but also vehicle components, such as pressed parts and chassis and drive systems. Located in component plant 02.20 is the BMW Group’s Centre of Competence for E-Drive Production, which provides BMW vehicle plants around the world with electric motors and high-voltage batteries for plug-in hybrids as well as fully electric models. It is under constant development and currently employs over 2,300 people.
In addition, Dingolfing creates the bodies-in-white of all the Rolls-Royce models. It is also home to what’s known as the Dynamics Centre, a large storage and trans-shipment point and the centrepiece of central aftersales logistics at the BMW Group, supplying BMW and MINI trading organisations with original BMW and MINI parts and accessories.
Source: BMW Group