Technology
Air Compressors: The Hidden Workhorses of Industrial Environments
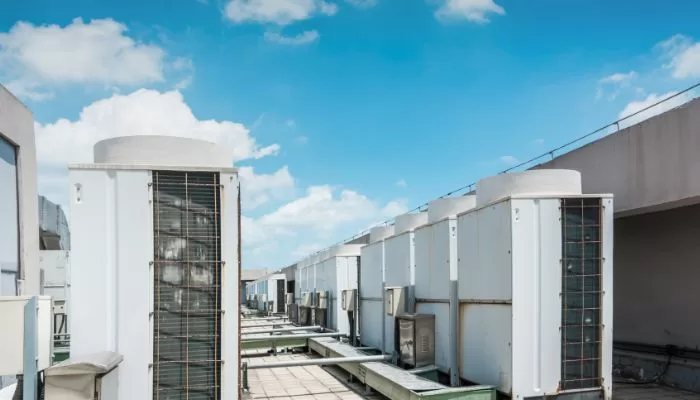
Introduction
You might not notice them, but air compressors are the tireless workhorses powering industrial facilities around the clock. Though they toil unseen in utility rooms and shops, these metal marvels supply the compressed air that keeps assembly lines humming, pneumatic tools cranking, and processes flowing smoothly from start to finish. Without these behind-the-scenes heroes generating vital air power, many manufacturing operations would grind to a halt. While their steadfast contributions go unappreciated by most, those in the know realize the modern factory floor couldn’t function without the range of rotary screw, reciprocating, centrifugal and specialty compressors operating reliably and efficiently. Their compressed air provides the hidden muscle that maintains productivity and keeps the wheels of industry turning. So, let’s shed some light on these overlooked pneumatic heroes to appreciate how integral reliable compressed air is for manufacturers.
Common Industrial Applications of Compressed Air
From power drills whirring on the assembly line to pneumatic actuators choreographing automated production, compressed air is the invisible life force animating activities throughout industrial facilities. This versatile air supply powers torque wrenches tightening bolts, air cylinders maneuvering materials, and drills boring precision holes. Compressed air aerates wastewater, cleans impurities, and agitates mixtures in treatment plants. It propels packaging down conveyors, blows plastic into mold cavities, and cools electrical control cabinets. Whether shooting a spray of paint, inflating a tire, or actuating a diaphragm valve, compressed air provides the main muscle for all kinds of pneumatic motion and mechanics. The range of uses across manufacturing sectors highlights how indispensable steady, quality compressed air is for industry.
Sizing and Selection Considerations
Choosing the right air compressor is more than just horsepower. Engineers weigh critical factors like required outlet pressure, peak and average airflow demands, 24/7 runtime, and noise restrictions. Undersizing could bottleneck production while oversized units guzzle unnecessary energy. Proper air compressor installation is also key – compressors need ample ventilation and clearance for maintenance access. With space at a premium, compact units are increasingly desirable. Whether installing a central compressor room or small shop versions, optimal placement boosts efficiency. Careful upfront calculations for pressure, flow rate, duty cycle, ambient conditions, and noise prevent powering problems down the road. Properly sizing and selecting the air compressor based on usage and installation needs delivers reliable compressed air where and when it’s needed.
Maintenance Needs for Reliability
To keep these workhorse compressors running reliably around the clock, diligent maintenance is a must. This includes frequently changing inlet air filters to maintain proper airflow and preventing contaminants from entering the system. Regular oil checks and changes remove sludge and debris to protect integral compressor components. Inspecting distribution piping and fittings for leaks ensures compressed air isn’t wasted. Monitoring outlet pressure detects issues before production is impacted. With multiple rotating parts subject to wear, even top-quality industrial compressors need TLC. Partnering with professional compressed air solutions providers for preventive maintenance and repairs reduces downtime risks. Proactive upkeep lets compressors operate more efficiently and reach their full service life, delivering value as a critical production asset.
Benefits of Professional Air System Management
Managing an extensive compressed air system is a complex, specialized task. The high-stakes industry solution? Partnering with professional compressed air system design and service teams. Experts can monitor demand fluctuations, stage multiple compressors efficiently, and implement system upgrades for peak performance. Preventive maintenance agreements ensure reliability while outsourcing labor burdens in-house. Compressor pros optimize piping schemes, storage capacity, and controls to maximize efficiency. They pinpoint leaks and right-size components to avoid wasted energy. With compressed air accounting for 10% of electricity in manufacturing, optimizing these complex systems cuts costs. Teaming up with specialty providers to proactively manage assets and air production delivers assurance that your operation has quality compressed air flowing reliably anytime it’s needed.
Conclusion
Whether powering tools, actuating machinery, or aerating wastewater, this adaptable utility makes modern manufacturing run. Compressed air propels assembly lines, molding equipment, and material handling activities that would otherwise rely on manual labor. To keep the compressed “fourth utility” flowing reliably, air compressors must be properly sized for the application’s pressure and flow rate demands. Partnering with specialists for ongoing compressor maintenance and system optimization sustains peak performance. By understanding compressed air’s many uses across industries and taking steps to manage compressed air systems proactively, manufacturers ensure this integral utility keeps day-to-day operations humming smoothly and efficiently. Though compressed air remains an unseen workhorse, its critical roles across industrial settings cannot be overstated.