Technology
The 5 Best Tools That’ll Make Your Business Run As Lean As Possible
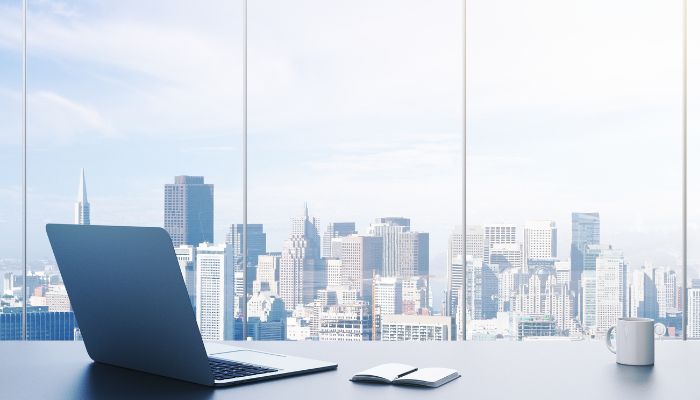
In an increasingly competitive business landscape, achieving operational efficiency is more crucial than ever. Adopting lean methodologies can transform a cluttered workflow into a streamlined powerhouse, significantly boosting productivity and reducing waste. This transformation is not just about cutting costs—it’s about optimizing every aspect of your operations to create value that resonates deeply with your customers.
The right tools can make this journey smoother and more effective, helping businesses of all sizes refine their processes and achieve sustainable growth. In this article, we explore the five best tools designed to make your business run as lean as possible. From visual management aids to systematic approaches to error-proofing, each tool offers a unique angle on cutting excess and enhancing efficiency, setting your business on a clear path to success in today’s dynamic market environment.
1. Kanban Boards
Kanban boards are a visual tool used to optimize workflow and manage production processes. Originating from the Japanese automotive industry, Kanban helps teams visualize tasks or project stages on a board—typically divided into columns such as “To Do,” “In Progress,” and “Completed.” This visibility allows teams to monitor progress and identify bottlenecks in real-time, ensuring that work flows efficiently through various stages.
By limiting the number of tasks in progress, Kanban boards help reduce overloading team members and focus on completing current tasks before taking on new ones. This not only speeds up production but also improves the quality of work by reducing errors caused by multitasking.
2. Value Stream Mapping
Value Stream Mapping (VSM) is a fundamental tool in the lean management toolkit, crucial for businesses aiming to enhance efficiency and reduce waste. It involves diagramming the flow of materials and information across the processes that lead to the delivery of a product or service. By using a value stream map template, businesses can visualize the entire process from start to finish, highlighting the value-adding as well as the non-value-adding activities.
Utilizing a value stream map template helps standardize the mapping process, ensuring consistency and clarity across different teams and projects within the organization. This approach allows stakeholders to pinpoint inefficiencies such as delays, redundancies, and bottlenecks in the production or service cycles.
With this detailed insight, companies can strategically target specific areas for improvement, streamline workflows, and ensure that every step of the process adds value to the customer. Ultimately, Value Stream Mapping drives better performance, enhances product quality, and leads to significant cost savings, making it an indispensable tool for businesses committed to operating as lean as possible.
3. 5S System
The 5S System is a methodical approach rooted in Japanese management philosophy that is instrumental in maintaining an organized, efficient, and safe environment. This tool is essential for businesses striving to optimize their operations under lean principles. The five steps—Sort, Set in Order, Shine, Standardize, and Sustain—are designed to improve workplace organization and efficiency systematically.
Sort involves removing unnecessary items from the workplace, Set in Order ensures every necessary item has a designated place, Shine focuses on regular cleaning and inspection, Standardize creates consistent ways to maintain cleanliness and order, and Sustain involves developing habits to maintain the standards.
By implementing the 5S System, businesses can significantly reduce the waste of resources and time spent searching for tools or equipment, thereby enhancing overall productivity. Moreover, it promotes a safer work environment by eliminating unnecessary clutter and potential hazards. Regularly applying these principles can foster a culture of discipline and continuous improvement, crucial for maintaining operational efficiency and making your business run as lean as possible.
4. Six Sigma
Six Sigma is a meticulous, data-driven approach that aims to enhance business processes by eliminating defects and reducing variability. It employs a set of quality management methods, mainly empirical, statistical analysis, and creates a special infrastructure of people within the organization who are experts in these methods. Each Six Sigma project carried out within an organization follows a defined sequence of steps and has quantified financial targets (cost reduction or profit increase).
The core philosophy of Six Sigma revolves around five key steps: Define, Measure, Analyze, Improve, and Control (DMAIC). This methodology helps businesses identify the causes of defects and the variables affecting key processes, ultimately providing them with the knowledge to sustain quality improvements over time.
By applying Six Sigma tools, companies can closely align their processes with customer expectations, leading to improved customer satisfaction, reduced cycle times, and lower defect rates in their products or services. For businesses looking to run as lean as possible, implementing Six Sigma can lead to substantial efficiency gains and a strong competitive advantage in the market.
5. Poka-Yoke (Error Proofing)
Poka-Yoke, or error-proofing, is a lean tool designed to prevent and eliminate errors. This technique involves designing processes in such a way that it is impossible to make mistakes. For example, using color-coding, shapes, or sizes that ensure parts can only be assembled in the correct way.
By implementing Poka-Yoke devices or methods, businesses can avoid costly mistakes and ensure that products are manufactured or services are performed correctly the first time. This not only saves time and resources but also enhances product reliability and customer trust.
Utilizing these five lean tools can dramatically transform the efficiency and effectiveness of your business operations. From the visual management capabilities of Kanban boards to the profound insights provided by Value Stream Mapping, each tool offers unique benefits that can help streamline your processes, eliminate waste, and maximize value to your customers. As businesses continue to navigate a world where efficiency is paramount, these tools provide the methodologies needed to stay competitive and thrive. Implementing lean tools isn’t just about cutting costs—it’s about creating a culture of continuous improvement and excellence that can lead to lasting success.